Gaso 3364 (55T-3)
(3364-7, 3365-5SC, 3364-6, 3364-3, 3364-2, 3364-1)
Triplex Plunger Pump
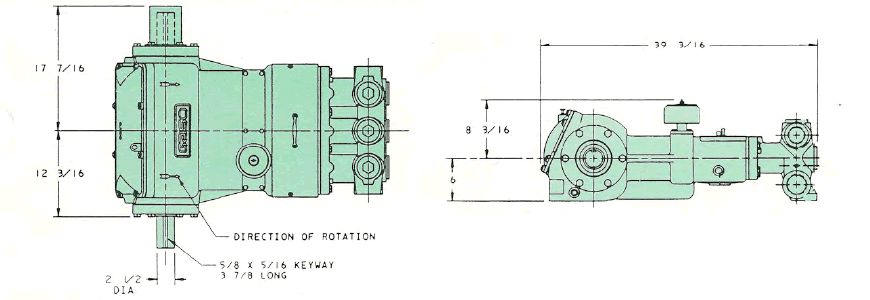
Specifications
No. of Plungers - 3
Stroke Length - 3"
Plunger Load - 4370 lbs.
Crankshaft Pin Dia. - 3.50"
Oil Capacity - 2 1/2 U.S. Gallons
Pump Weight - 720 lbs.
Connections:
- Model 3364-3
- Standard
2 1/2 " NPT suction
2" NPT discharge - Optional
2" - 150# ANSI suction
2" - 2000# API RT J discharge
- Standard
- Model 3364-4, 5 & 7
- Optional
2 1/2 NPT suction
2" NPT discharge - Optional
2" - 150# ANSI suction
2" - 600# ANSI discharge
- Optional
Standard Materials for Fluid End Bodies:
3364-3, 3354-4, 3364-7 - Cast Nickel Aluminum Bronze
3364-5 - Cast Ductile Iron
PUMP MODEL |
PLGR. DIA. IN. |
MAX. PRESS PSI |
DISP. GAL. PER REV. |
DISPLACEMENT | |||||||||
100RPM | 200RPM | 300 RPM | 400RPM | 500 RPM | |||||||||
GPM | BPD | GPM | BPD | GPM | BPD | GPM | BPD | GPM | BPD | ||||
3364-3 | 1 1/4 | 1815 | .0478 | 4.8 | 165 | 9.6 | 490 | 14.3 | 490 | 19.1 | 655 | 23.9 | 819 |
1 1/2 | 1815 | .0688 | 6.9 | 235 | 13.8 | 705 | 20.6 | 705 | 27.5 | 945 | 34.4 | 1179 | |
1 3/4 | 1815 | .0937 | 9.4 | 320 | 18.7 | 965 | 28.1 | 965 | 37.5 | 1285 | 46.8 | 1606 | |
3364-4 | 1 3/4 | 1390 | .0937 | 9.4 | 320 | 18.7 | 965 | 28.1 | 965 | 37.5 | 1285 | 46.8 | 1606 |
2 | 1390 | .1224 | 12.2 | 420 | 24.5 | 1260 | 36.7 | 1260 | 49.0 | 1680 | 61.2 | 2098 | |
2 1/4 | 1100 | .1549 | 15.5 | 530 | 31.0 | 1595 | 46.5 | 1595 | 61.9 | 2125 | 77.4 | 2655 | |
3364-5 | 1 3/4 | 1390 | .0937 | 9.4 | 320 | 18.7 | 965 | 28.1 | 965 | 37.5 | 1285 | 46.8 | 1606 |
2 | 1390 | .1224 | 12.2 | 420 | 24.5 | 1260 | 36.7 | 1260 | 49.0 | 1680 | 61.2 | 2098 | |
2 1/4 | 1100 | .1549 | 15.5 | 530 | 31.0 | 1595 | 46.5 | 1595 | 61.9 | 2125 | 77.4 | 2655 | |
3364-7 | 2 | 1390 | .1224 | 12.2 | 420 | 24.5 | 1260 | 36.7 | 1260 | 49.0 | 1680 | 61.2 | 2098 |
2 1/4 | 1100 | .1549 | 15.5 | 530 | 31.0 | 1595 | 46.5 | 1595 | 61.9 | 2125 | 77.4 | 2655 | |
2 1/2 | 890 | .1912 | 19.1 | 655 | 38.2 | 1970 | 57.4 | 1970 | 76.5 | 2620 | 95.6 | 3277 | |
MAX. BRAKE HORESPOWER REQUIRED | 11.0 | 22.0 | 33.1 | 44.1 | 55.2 |
Careful planning of the plant layout will save considerable time and expense, both initially when the installation is made and later during the operation of the plant In selecting the location for the pump, consideration should be given to the fact that a positive suction head at the pump inlet contributes toward the pump efficiency. However, the layouts of the piping, the arrangement of the fittings, and restrictions in the suction and discharge lines have even more effect For this reason, all fittings and valves should be full opening; all bends should be of long radius or should be eliminated where possible. Long radius 45° ells should be used, particularly if installed near the fluid cylinder. The following points outline the basic requirements for an installation that will contribute greatly toward good pump operation.
A. Suction Line
- The suction line must not be smaIIer than the suction intake of the fluid cylinder and may be larger. The Iength of the suction line should be held to a minimum and should run straight from the suppIy tank to the pump.
- When bends are required, They should be made with long radius 45° ells. Do not use a bend directly adjacent to the fluid cylinder. Avoid using any 90° bends if at all possible.
- Provide a full opening gate valve in the suction line adjacent to the supply tank to permit the line to be drained when necessary. Do not use any type of restricting valve.
- Do not use meters or other restrictions in the suction line. Eliminate any rise of summit in the suction line where air or vapor can collect.
- Pulsation dampening devices are strongly recommended.
- When necessary to manifold a number of pumps to a common suction, the diameter of the manifold and suction pipe leading from the supply tank must be such that it has a cross-sectional area equal, to or greater than, the area of the combined individual suction pipes.
- When a charging or booster pump is used in the suction line, it must have a capacity equal to twice that of the pump output. This is necessary to provide a charging pump with an output great enough to meet the peak volume requirements of the plunger pump during the suction stroke and not act as a restriction in the line.
- All piping, both suction and discharge must be solidly and independently supported. The first support must be as close to the pump as practical. This is necessary to prevent placing the pump in a strain and to keep any vibration in the system from acting directly on the pump.
B. Discharge Line
- Use a pulsation dampener or a desurger in the discharge line. It should be placed in the line as near the fluid cylinder as possible and ahead of any bend in the line.
- Do not reduce the size of the discharge line below that of the pump outlet until the line has passed through the desurger, and is away from the pump approximately 20 feet (6m).
- Any bend in the discharge line should be made with a long radius 45° ell. Do not use a bend directly adhacent to the fluid cylinder, particularly a 90° bend.
- A pressure relief valve should be installed in the discharge line. The relief vale should be set to operate at a pressure no greater than 25% above the maximum rated pressure for the plunger size being used. It should be installed in the line ahead of any valve and piped so that any flow is returned to the supply tank rather than the suction line. This will prevent possible damage to the suction line and suction dampener.
C. Power End
- The pump must be mounted level and should be grouted in and free from strain. This applies to a skid-mounted pump or a pump mounted directly on a conctrete base.
- The sheave of a belt driven pump must be correctly aligned with the prime mover sheave. Care must be used to prevent over-tightening as this will shorten belt life, place the puimp in a strain and cause undue additional loads on the crankshaft and bearings. Sheave sizes should not be smaller than the approved diameter.
- When connecting a direct-driven pump, the shafts must be correctly aligned. Couplings should not be expected to compensate for avoidable misalignment. With Thomas Flexible couplings, angular misalignment should not exceed one-half degree. Offset misalignmentof the centerlines of the two shafts should not exceed .015" (.381 mm). Actually, misalignment should be as small as practical.
- Provisions should be made to stop the pump automatically in the event of supply fluid failure. A pump should not be run dry, as this causes wear on the packing.
- The pump has been drained of oil after testing at the factory and MUST be filled with the proper oil (see Lubrication section) before starting. The rust inhibiting oil coating inside the power end need not be removed before filling; however it is recommended that the power end be checked to make sure dirt or contamination has not entered during shipment.
D. Fluid End
- The fluid cylinder is shipped assembled to the pump complete with valves and cover plates. The stuffing boxes, plungers, and related items have also been assembled and tested with the pump (unless otherwise specified) and require no further assembly. Before the pump is started, these parts should be checked for tightness as well as for possible damage during shipment.
- Thoroughle clean the suction line piping before starting the pump. Weld spatter, slag, mill scale, etc., will damage a pump in a short time.
E. Plunger Packing
The recommended style of packing has been installed and run at the plant. It does, however, require further "setting up" as the pump is started and brought up to pressure. Refer to Plunger Packing Installation section for the correct procedure for packing used.
F. Plunger Packing Lubrication
- Automatic packing lubricators are beneficial on all installations and are required on pumps operating at high pressure (1200 psi [85kg/cm2] and up) to obtain good packing life.
- When an automatic lubricator is used in water and power oil service, use Rock Drill (Air Drill) oil of proper viscosity. For butane-propane service, use NATURAL castor oil. Set lubricator to feed 5-7 drops per minute.
G. Suction Pulsation Dampeners
- Low Pressure - Plastic Body
a. Some Gaso plunger pumps are equipped with suction pulsation dampeners. These dampeners do an excellent job when properly charged and should be kept filled during operation.
!ATTENTION!
At suction pressures over 10 psi (.7kg/cm2), the dampener should be deflated prior to bleeding off the suction pressure to prevent damage to the diaphragm.
b. The plastic dampener body has an instruction decal attached, which lists the following installation and charging procedures.
!ATTENTION!
HANDLE WITH CARE.
This is a plastic part and can be broken.
c. Tighten capscrews with 10 to 12 ft-lbs. of torque.
!ATTENTION!
Use thread-sealing compound on check valve and tighten until snug.
OVERTIGHTENING WILL DAMAGE BODY.
d. With pump operating - Charge dampener until bottom of diaphragm is visible through sight glass. Proper charge is when bottom of diaphragm is between center and top of sight glass.
2. High Pressure - Aluminum Body
a. For pressures in excess of 20 psi (1.406 kg/cm2) and up to 70 psi (10.545 kg/cm2), it is necessary to use the National Oilwell Varco high-pressure suction dampener.
b. The high-pressure dampener is charged in a similar manner to the low-pressure plastic dampener, using air or nitrogen to charge the diaphragm and maintain its position in relation to the sight glass.
c. The following procedures should be used to service this dampener:
(1) The dampener is fitted to an adapter that may be either welded into an existing line or be a part of a separate dampener housing. Place a gasket on each side of the diaphragm retaining plate and place on the adapter.
(2) The dampener spacer is then placed on top of the retainer plate with the grooved side up and the flat side against the retainer gasket.
(3) The diaphragm fits into the groove on the spacer with the curved portion of the diaphragm above the spacer.
(4) Apply a continuous 1/8" diameter bead of silicone rubber on the outer edge of the diaphragm after it has been positioned into the spacer. This silicone rubber (GE Silicone Rubber or Dow-Corning Silastic) is readily available at most hardware stores. Assemble the body cover within ten minutes after applying the silicone rubber.
(5) Fit the dampener cover over the diaphragm and assemble the capscrews. Tighten the capscrews evenly to approximately 80 ft-lbs. of torque.
(6) Install the sight glasses, one in each side of the cover. Be sure to seat the sight glass packing carefully into the groove on the cover, as this must be an airtight connection.
(7) The air check valve has a pipe thread and must be made up into the cover airtight. Use a good pipe thread sealant to promote sealing.

The following must be checked for the prevention of trouble or to correct trouble that may arise.
A. Operation Checklist
- Pump must be set level for proper lubrication.
- Make sure pump is filled with clean oil of the porper viscosity (see Lubrication Section )
- Do not over-speed the pump.
- Do not use a smaller diameter sheave than is recommended for the pump.
- Make sure all safety shutdown switches are operating properly.
- Keep all suction and discharge line valves fully open.
- If a bypass is used to regulate output, make sure it is set properly.
- Make sure the pressure relief valve is set properly.
- Do not exceed the pressure rating of the pump for the particular plunger size.
- Make sure the suction line is tight, as air entering the suction line will cause severe hammering and knocking of the pump.
- Make sure plunger and intermediate rod connections are tight and locked.
- Check the plunger packing for correct adjustment (see Plunger Packing Installation)
- Check the suction and discharge dampeners for proper charge, as this is very important for long life and good pump operation.
- Make sure fasteners holding the cylinder in place are tight.
The Gaso 3364 multiplex pump is "splash" lubricated. The main bearings and crankshaft bearings are fed by splash. Crossheads and crosshead pin bushings are fed through holes in the crossheads and splash through the crosshead weighs. Intermediate rods are lubricated from the splash they receive from the crosshead.
U.S. Units of Measure |
|
Temperature | AGMA Industrial Gear Oil |
+50°F to +155°F | AGMA No. 6 EP or ASTM/ISO Grade No. 320 (viscosity 1335 to 1632 SSU 100°F) |
+20°F to +100°F | AGMA No. 5 EP or ASTM/ISO Grade No. 220 (viscosity 918 to 1122 SSU 100°F) |
-20°F to +60°F | AGMA No. 2 EP or ASTM/ISO Grade No. 68 (viscosity 284 to 347 SSU 100°F) |
Approximate crankcase Capacity - Quarts: 10
(For exact amount observe dip stick provided with pump)
Metric Units of Measure |
|
Temperature | AGMA Industrial Gear Oil |
+10°C to +68°C | AGMA No. 6 EP or ASTM/ISO Grade No. 320 (viscosity 228-352 cSt at 37.8°C) |
-7°C to +38°C | AGMA No. 5 EP or ASTM/ISO Grade No. 220 (viscosity 198-242 cSt at 37.8°C) |
-29°C to +16°C | AGMA No. 2 EP or ASTM/ISO Grade No. 68 (viscosity 61-75 cSt at 37.8°C) |
Approximate crankcase Capacity - Liters: 9.5
(For exact amount observe dip stick provided with pump)
Oil must pour freely at minimum operating temperature. Change oil every six months or as frequently as operating conditions require maintaining a clean, sludge-free oil of proper viscosity.